From heat pump trainee to installer: help your trainees succeed
27 Feb 2025
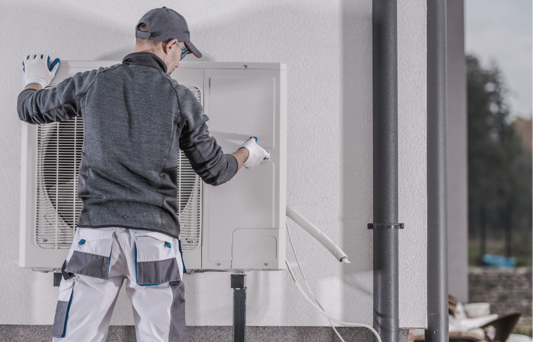
The heat pump industry has seen remarkable growth in recent years, fueled by government incentives like the Boiler Upgrade Scheme (BUS) and a growing demand for low-carbon heating solutions.
As a consequence, the workforce needed for the heat pump sector is projected to grow significantly, with estimates suggesting a requirement of over 30,590 trained individuals by 2028. Despite this demand, the Heat Pump Association (HPA) reports that while training figures are rising - 7,800 completed training in 2023, and over 7,000 in 2024 - almost half of trained engineers have yet to complete an installation.
Bridging this gap is crucial for meeting the UK's heat pump deployment targets. Training centres play an essential role in equipping heating engineers with not only technical skills but also the business acumen, industry connections and imperatively, the confidence required to succeed.
From training to installation: what’s stopping new heat pump engineers?
A range of factors are preventing trained installers from becoming MCS registered heat pump engineers.
Research from Nesta helps us to understand the disconnect - revealing the challenges that newly qualified engineers face:
● Skills confidence gap – many trainees feel unprepared and unsupported when facing real-world installations
● Lack of confidence in the technology – some heating engineers remain doubtful about heat pumps’ reliability and performance, despite increasing evidence in their favor
● MCS certification hurdle – the process of obtaining MCS accreditation can feel daunting, requiring arduous paperwork and strict adherence to quality management systems
● Administrative overload – for those who are new to the industry, the complexity of surveying, planning and quoting can be overwhelming
● Difficulty securing first customers – newly qualified installers often struggle to find clients willing to take a chance on a less experienced engineer
● Market domination by large companies – major energy providers monopolise the market, leveraging their brand recognition and ability to offer more competitive prices
To effectively tackle these barriers, the industry needs a collaborative approach involving training providers, manufacturers, accrediting bodies like MCS and installers themselves. Training centres can help specifically by better preparing trainees to confidently transition from trainee to heat pump installer.
Here are some top tips for centres helping heat pump trainees become successful installers.
Go beyond technical training
While a Level 3 heat pump installation qualification - partnered with the Level 3 low temperature heating and hot water systems in dwellings qualification - provides essential technical knowledge, trainees often need guidance on real-world application. The reality of working in a home is quite different to that of a classroom.
Training centres can help this transition by incorporating practical, hands-on training in realistic installation environments, wherever possible. While a well set up rig in a classroom is great, site visits can help trainees understand the common challenges they may face on the job. Commissioning, the process of verifying that a newly installed heat pump system is functioning correctly according to the manufacturer's specifications – an important final quality check – is an area where many installers lack confidence. This need could be addressed with blended learning, both hands-on training in real homes and classroom education.
You can also encourage your trainees to do some homework, such as talking to their local merchants and gathering key information about what goes into specifying and installing a heat pump – a solid understanding of product specifications and pricing is crucial. Some manufacturers offer heat pump packs which include everything needed for an installation. Alternatively, installers may prefer to put their own kit list together.
Point them in the direction of user-friendly information such as the heat pump service checklist from HPA.
Get them to speak to their friends, family and existing clients to find out what they know and feel about heat pumps, this will help them understand the barriers they might face as well as start conversations with potential future heat pump customers.
Explain the benefits of networking with other installers (both online and in person) - connecting with other industry professionals can provide invaluable insights and support. Social media groups host active discussions on heat pump installation, while local trade groups offer networking opportunities.
Strengthen manufacturer partnerships
Manufacturers are eager to work with trained professionals and create long-term partnerships with qualified installers.
Some LCL Awards centres are also manufacturers, NIBE, Daikin and Worcester Bosch to name a few. Other training centres can help facilitate manufacturer relationships by building their own relationships, particularly if they're using particular brands of heat pump in the centre. Direct installers towards the often free product training that most of the major manufacturers provide.
Apart from getting to grips with the nuances of certain products, partnering with manufacturers can also offer other benefits to installers, such as technical support, warranties, MCS umbrella schemes and even assistance during the first install. This is a great opportunity for installers to learn about the nuances of specific of heat pump systems.
Guide trainees through MCS certification options
The Microgeneration Certification Scheme (MCS) is often seen as a major hurdle for new heat pump installers. Educating trainees on different pathways to ensuring installs are MCS certified; a prerequisite of accessing the Boiler Upgrade Scheme (BUS), is key.
Starting under an umbrella scheme while building a portfolio of successful installations can be a good option for new installers in particular. This experience can be extremely useful if they later decide to pursue their own MCS certification. Installers should reach out to their preferred manufacturer or merchant to understand what umbrella schemes are on offer.
Support trainees to find an umbrella scheme that offers:
● Quality management system templates to streamline compliance
● Design support and technical guidance before and during installations
● Insurance coverage for added security
● Marketing assistance to grow business profile and customer base
● Ongoing professional development training to refine skills and stay updated
Help trainees build a business model
Success in the heat pump market isn’t just about technical expertise - it requires a strategic business approach for long-term success. Training centres might consider offering workshops or resources on:
● Forming partnerships with local architects, builders and renewable energy firms
● Investing in the right tools for accurate diagnostics and efficient installations. The latest digital tools coming to market include mobile apps that transform heat pump specification and installation, streamlining tasks such as heat loss calculations, system design and project management
● Effective marketing, including branding, website development and social media presence
● Joining trade associations to stay updated with industry trends and networking opportunities
Encourage trainees to think of heat pump installation as a new business venture rather than just an add on technical skill.
Promote continuous professional development
By fostering a culture of continuous learning, training centres can support newly qualified installers to remain competitive and adaptable in the field. The renewable heating industry is evolving rapidly, with new technologies and regulations emerging regularly.
Training centres should encourage trainees to keep their skill-set up to date by:
● Attending trade shows and exhibitions, maintaining awareness of the latest innovations and network with industry leaders
● Engaging in online learning and discussions such as interactive webinars, social media groups (where industry discussions take place) and manufacturer-led training events
● Subscribing to trade publications for updates on best practices, industry regulations and financial incentives
Qualified and ready - now it’s time to install
The transition from heat pump trainee to active installer doesn’t happen overnight, but training centres play an essential role in bridging the gap from trainee to installer. By focusing on hands-on experience, manufacturer relationships, business training and encouraging ongoing professional development, we can equip LCL Awards qualified installers with the confidence and skills needed to thrive.
This is a great opportunity for training centres, and those that go the extra mile when it comes to helping their customers use the skills they’ve learned will attract new and repeat custom: trades people that do well tend to keep training; either themselves or their staff as their business grows.
The heat pump industry has seen remarkable growth in recent years, fueled by government incentives like the Boiler Upgrade Scheme (BUS) and a growing demand for low-carbon heating solutions.
As a consequence, the workforce needed for the heat pump sector is projected to grow significantly, with estimates suggesting a requirement of over 30,590 trained individuals by 2028. Despite this demand, the Heat Pump Association (HPA) reports that while training figures are rising - 7,800 completed training in 2023, and over 7,000 in 2024 - almost half of trained engineers have yet to complete an installation.
Bridging this gap is crucial for meeting the UK's heat pump deployment targets. Training centres play an essential role in equipping heating engineers with not only technical skills but also the business acumen, industry connections and imperatively, the confidence required to succeed.
From training to installation: what’s stopping new heat pump engineers?
A range of factors are preventing trained installers from becoming MCS registered heat pump engineers.
Research from Nesta helps us to understand the disconnect - revealing the challenges that newly qualified engineers face:
● Skills confidence gap – many trainees feel unprepared and unsupported when facing real-world installations
● Lack of confidence in the technology – some heating engineers remain doubtful about heat pumps’ reliability and performance, despite increasing evidence in their favor
● MCS certification hurdle – the process of obtaining MCS accreditation can feel daunting, requiring arduous paperwork and strict adherence to quality management systems
● Administrative overload – for those who are new to the industry, the complexity of surveying, planning and quoting can be overwhelming
● Difficulty securing first customers – newly qualified installers often struggle to find clients willing to take a chance on a less experienced engineer
● Market domination by large companies – major energy providers monopolise the market, leveraging their brand recognition and ability to offer more competitive prices
To effectively tackle these barriers, the industry needs a collaborative approach involving training providers, manufacturers, accrediting bodies like MCS and installers themselves. Training centres can help specifically by better preparing trainees to confidently transition from trainee to heat pump installer.
Here are some top tips for centres helping heat pump trainees become successful installers.
Go beyond technical training
While a Level 3 heat pump installation qualification - partnered with the Level 3 low temperature heating and hot water systems in dwellings qualification - provides essential technical knowledge, trainees often need guidance on real-world application. The reality of working in a home is quite different to that of a classroom.
Training centres can help this transition by incorporating practical, hands-on training in realistic installation environments, wherever possible. While a well set up rig in a classroom is great, site visits can help trainees understand the common challenges they may face on the job. Commissioning, the process of verifying that a newly installed heat pump system is functioning correctly according to the manufacturer's specifications – an important final quality check – is an area where many installers lack confidence. This need could be addressed with blended learning, both hands-on training in real homes and classroom education.
You can also encourage your trainees to do some homework, such as talking to their local merchants and gathering key information about what goes into specifying and installing a heat pump – a solid understanding of product specifications and pricing is crucial. Some manufacturers offer heat pump packs which include everything needed for an installation. Alternatively, installers may prefer to put their own kit list together.
Point them in the direction of user-friendly information such as the heat pump service checklist from HPA.
Get them to speak to their friends, family and existing clients to find out what they know and feel about heat pumps, this will help them understand the barriers they might face as well as start conversations with potential future heat pump customers.
Explain the benefits of networking with other installers (both online and in person) - connecting with other industry professionals can provide invaluable insights and support. Social media groups host active discussions on heat pump installation, while local trade groups offer networking opportunities.
Strengthen manufacturer partnerships
Manufacturers are eager to work with trained professionals and create long-term partnerships with qualified installers.
Some LCL Awards centres are also manufacturers, NIBE, Daikin and Worcester Bosch to name a few. Other training centres can help facilitate manufacturer relationships by building their own relationships, particularly if they're using particular brands of heat pump in the centre. Direct installers towards the often free product training that most of the major manufacturers provide.
Apart from getting to grips with the nuances of certain products, partnering with manufacturers can also offer other benefits to installers, such as technical support, warranties, MCS umbrella schemes and even assistance during the first install. This is a great opportunity for installers to learn about the nuances of specific of heat pump systems.
Guide trainees through MCS certification options
The Microgeneration Certification Scheme (MCS) is often seen as a major hurdle for new heat pump installers. Educating trainees on different pathways to ensuring installs are MCS certified; a prerequisite of accessing the Boiler Upgrade Scheme (BUS), is key.
Starting under an umbrella scheme while building a portfolio of successful installations can be a good option for new installers in particular. This experience can be extremely useful if they later decide to pursue their own MCS certification. Installers should reach out to their preferred manufacturer or merchant to understand what umbrella schemes are on offer.
Support trainees to find an umbrella scheme that offers:
● Quality management system templates to streamline compliance
● Design support and technical guidance before and during installations
● Insurance coverage for added security
● Marketing assistance to grow business profile and customer base
● Ongoing professional development training to refine skills and stay updated
Help trainees build a business model
Success in the heat pump market isn’t just about technical expertise - it requires a strategic business approach for long-term success. Training centres might consider offering workshops or resources on:
● Forming partnerships with local architects, builders and renewable energy firms
● Investing in the right tools for accurate diagnostics and efficient installations. The latest digital tools coming to market include mobile apps that transform heat pump specification and installation, streamlining tasks such as heat loss calculations, system design and project management
● Effective marketing, including branding, website development and social media presence
● Joining trade associations to stay updated with industry trends and networking opportunities
Encourage trainees to think of heat pump installation as a new business venture rather than just an add on technical skill.
Promote continuous professional development
By fostering a culture of continuous learning, training centres can support newly qualified installers to remain competitive and adaptable in the field. The renewable heating industry is evolving rapidly, with new technologies and regulations emerging regularly.
Training centres should encourage trainees to keep their skill-set up to date by:
● Attending trade shows and exhibitions, maintaining awareness of the latest innovations and network with industry leaders
● Engaging in online learning and discussions such as interactive webinars, social media groups (where industry discussions take place) and manufacturer-led training events
● Subscribing to trade publications for updates on best practices, industry regulations and financial incentives
Qualified and ready - now it’s time to install
The transition from heat pump trainee to active installer doesn’t happen overnight, but training centres play an essential role in bridging the gap from trainee to installer. By focusing on hands-on experience, manufacturer relationships, business training and encouraging ongoing professional development, we can equip LCL Awards qualified installers with the confidence and skills needed to thrive.
This is a great opportunity for training centres, and those that go the extra mile when it comes to helping their customers use the skills they’ve learned will attract new and repeat custom: trades people that do well tend to keep training; either themselves or their staff as their business grows.